
Unlocking more sustainable futures with green chemistry
Using chemistry to help reach sustainability goals is becoming an increasingly attractive research area. From solving global plastic pollution to improving the performance of rechargeable batteries found in electric cars, ‘green chemistry’ is a truly promising topic.
This article was researched and written by Isabel Williams, a former Masters Student at Oxford University’s Department of Biology.
Tackling the plastic pollution problem

But why is plastic such a problematic material? To find out why and to begin to tackle these problems, one needs to look at the material’s chemistry.
Plastics are made from synthetic ‘polymers’. Polymers are made from small molecular building blocks, called ‘monomers’, forming a large molecule resembling beads on a string. In plastics, these monomers are usually derived from non-renewable sources such as petrochemicals, making the production of plastic polymers highly unsustainable since they rely on fossil fuels. Additionally, due to the strong bonds between their monomers, synthetic polymers can persist and pollute the environment for hundreds of years before breaking down.
The solution: replacing plastics with ‘greener’ polymers

Researchers at the University of Oxford’s Department of Chemistry are utilising a green chemistry approach to tackle plastic pollution. The aim? To phase out existing polymers and plastics and replace them with greener, more sustainable alternatives.
One avenue being explored is the production of polymers from renewable, bio-derived materials, rather than petrochemicals. Dr Matilde Concilio, a Postdoctoral Research Associate in Professor Charlotte Williams’ laboratory, works on making bio-derived polymers from commercially available resources. By using chemicals already commercialised, safety-checked, and approved, the hope is that any products or processes developed in this way will be swiftly accepted and adopted by industry. With bio-derived plastics accounting for only 1.5% of global plastic production in 2021, there is enormous potential for these materials to upscale and ultimately replace their less-sustainable competitors.
I’m convinced that polymers are the future, but only if you do it in a sustainable way.
Dr Matilde Concilio, Department of Chemistry
Dr Concilio’s bio-derived polymers are not only made from renewable sources but are also more sustainable from a processing standpoint. Usually, monomers need to be purified many times to achieve a high-quality final product. This is both energetically costly and expensive.
‘So, to make it more sustainable, what I’m trying to do is use monomers that don’t need to be purified’ Dr Concilio explains. This way, less energy, time, and money are spent on the polymerisation process.
Key to the development and uptake of these new polymers is ensuring that their material properties are as good as, if not better than, current petrochemically-derived options. This is essential if these new materials are to be adopted at scale within plastics industries.
Ultimately, what we want to do is phase out [the current plastics], so that our plastics, which we’re quite heavily reliant on as a society, come from renewable sources.
Dr Gregory Sulley, Department of Chemistry
‘One of the main targets for us is to try and property-match to the incumbent materials,’ says Dr Gregory Sulley, another Postdoctoral Research Associate in Professor Charlotte Williams’ laboratory. ‘Ultimately, what we want to do is phase out [the current plastics], so that our plastics, which we are quite heavily reliant on as a society, come from renewable sources.’
With continued work and collaboration, hopefully, sustainable plastics will go on to replace their more unsustainable alternatives, making plastic pollution a problem of the past. With any luck, the sight of plastic in our landfills, oceans, and beaches will soon be a distant memory.
Tailor-made polymers for energy storage solutions:
Similar green chemistry approaches are being applied to solve problems in energy storage. For instance, rechargeable batteries require their components to be in contact with one another to function. However, this is complicated by the fact that some of the components change volume as the battery is charged and discharged. With these batteries used in electric cars, solar panels, and wind turbines, overcoming this problem is a huge priority to help reach Net Zero emission targets.
So, how do you solve this problem? Enter polymers.
Dr Georgina Gregory. Photo credit: Royal Society.
This application-driven design is integral to Dr Gregory’s work to improve the design of polymers so that they can overcome the current limitations of rechargeable batteries.
‘The polymer, in some respects, comes in as a way of holding it all together’ Dr Gregory explains. This means the polymer needs to be:
- Adhesive: to stick everything together in the battery;
- Slightly flexible: to accommodate the changes in volume;
- Ionically conductive: the polymer needs to allow ions (electrically-charged atoms) to flow through the battery.
With these three properties in mind, the researchers set out to precisely design a polymer for use in batteries. By specifically selecting building blocks possessing these properties, and utilising their ability to tightly control the polymerisation process, they were able to tailor the product to the problem.
A sustainable solution
The major global problem is replacing the plastics that we currently have. They are in absolutely everything, even things that you don’t even know they’re in.
Dr Georgina Gregory, Department of Chemistry
You would think with these many criteria, sustainability would fall to the back-burner. However, sustainability is still central to Dr Gregory’s tailor-made polymers.
‘I’m always trying to pick building blocks that are bio-based, so polymers won’t have a negative impact at end-of-life.’ Dr Gregory is referring to the fact that bio-derived polymers, in contrast to traditional synthetic polymers, can be quickly broken down using water. Consequently, the material doesn’t remain in the environment for as long, and degrades at a faster rate into smaller, non-toxic parts.
Additionally, the bio-derived polymers lend themselves to chemical recycling. Here, you ‘unzip’, or ‘depolymerise’ the polymer back to the monomers, or original building blocks, then use these monomers to make new polymers. Therefore, the tailor-made, bio-derived polymers don’t contribute to the global issue of plastic pollution.
This ability to produce ‘tailored’ polymers is a special skill, one that is enabling University of Oxford chemists to tackle the crucial engineering challenges that are currently holding back the key technologies we need to achieve Net Zero.
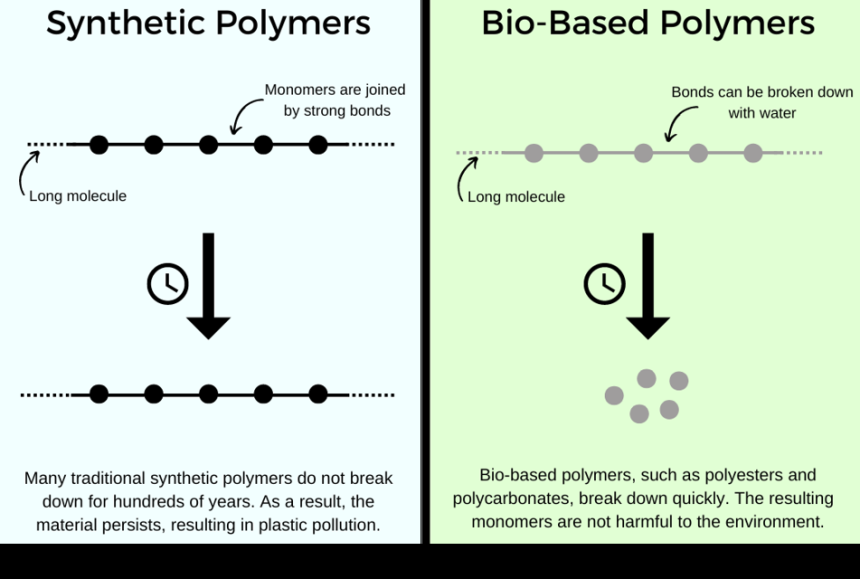
Taking the hazards out of a hazardous production process
Sometimes, it isn’t so much the end product but the production process that creates environmental problems. Take fluorochemicals, for instance. This group of chemicals have a wide range of important applications – including polymers, agrochemicals, pharmaceuticals, and the lithium-ion batteries in smartphones and electric cars – and had a $21.4 billion global market in 2018. But currently, all fluorochemicals are generated from the toxic and corrosive gas hydrogen fluoride (HF) in a highly energy-intensive process. In addition, even with the best safety precautions, HF spills have occurred numerous times over the last decades, sometimes with fatal accidents and severe environmental impacts.
Thankfully, this may not be the case in the future, thanks to a new, safer approach developed by a team of University of Oxford chemists, alongside colleagues in Oxford spin-out FluoRok, University College London, and Colorado State University. The innovative method takes inspiration from the natural biomineralization process that forms teeth and bones.
Normally, HF itself is produced by reacting a crystalline mineral called fluorspar (CaF2) with sulfuric acid under harsh conditions, before it is used to make fluorochemicals. In the new method, fluorochemicals are made directly from CaF2, completely bypassing the production of HF: an achievement that chemists have sought for decades.
This advance builds on decades of research from the laboratory led by Professor Véronique Gouverneur FRS at the University of Oxford. ‘The direct use of CaF2 for fluorination is a holy grail in the field, and a solution to this problem has been sought for decades’ she says. ‘The transition to sustainable methods for the manufacturing of chemicals, with reduced or no detrimental impact on the environment, is today a high-priority goal that can be accelerated with ambitious programs and a total re-think of current manufacturing processes.’
By commercialising this technology, we aim to enable the development of safe, sustainable, and cost-effective synthesis of fluorocarbons worldwide. We hope that this study will encourage scientists around the world to provide disruptive solutions to challenging chemical problems, with the prospect of societal benefit.
Professor Véronique Gouverneur FRS, Department of Chemistry
In the novel method, solid-state CaF2 is activated by a biomineralization‑inspired process, which mimics the way that calcium phosphate minerals form biologically in teeth and bones. Professor Véronique’s team ground CaF2 with powdered potassium phosphate salt in a ball-mill machine for several hours, using a mechanochemical process that has evolved from the traditional way that we grind spices with a pestle and mortar.
The resulting powdered product, called FluoromixTM, allows over 50 different fluorochemicals to be made directly from CaF2, with yields of up to 98%.
Calum Patel, a DPhil student in the Department of Chemistry, and one of the researchers leading this work, says: ‘Mechanochemical activation of CaF2 with a phosphate salt was an exciting invention because this seemingly simple process represents a highly effective solution to a complex problem; however, big questions on how this reaction worked remained. Successful solutions to big challenges come from multidisciplinary approaches and expertise, I think the work really captures the importance of that.’
The process represents a paradigm shift for the manufacturing of fluorochemicals across the globe, and led to the creation of spin‑out company FluoRok in 2022. With the method being suitable for both academic and industrial applications, the research team hope it will ultimately lead to significant impacts in minimising carbon emissions (e.g. by shortening supply chains) and increasing the reliability of fluorochemical supply chains.
As Professor James Naismith, Head of the Mathematical, Physical and Life Sciences Division at Oxford University, says, these examples demonstrate how Oxford is leading the way to develop innovative solutions to our most pressing challenges. 'It is only through innovation that we can both improve the quality of life and stop damaging the planet' he says. 'Chemists at Oxford are leaders in green chemistry; the science behind sustainability. The range of work highlighted here includes materials from biology that could replace the fossil fuel-derived polymers modern life depends on, zero impact materials for lithium batteries, and replacing the use of waste-generating hazardous processes for chemicals which we can’t yet do without. The future is being made in Oxford by our talented researchers and students; this is a global effort with partnerships spanning the world.'
Green chemistry, also called sustainable chemistry, is defined as ‘the design of chemical products and processes that reduce or eliminate the use and generation of hazardous substances’ by the European Environmental Agency (EEA). Interest in this area has been increasing since the 1990s, with the US Environmental Protection Agency and the Royal Society of Chemistry’s journal, Green Chemistry, playing an important role.